|
|
|
|
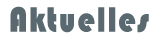 |
|
|
Neues, Termine und mehr |
|
|
|
EuroBLECH 2022
26. Internationale Technologiemesse
für Blechbearbeitung
25.-28. Oktober 2022 Messe Hannover |
|
|
|
Oktober
|
|
Beutler Nova AG erhält Innovationspreis
Industrie- und Handelskammer Zentralschweiz prämiert Schuler-Tochter für zwei neu entwickelte Stanzautomaten mit ServoDirekt-Technologie
Göppingen, 23.11.2016 Die Beutler Nova AG hat heute am Firmensitz im schweizerischen Gettnau den Innovationspreis der Industrie- und Handelskammer Zentralschweiz (IHZ) erhalten. Das Tochterunternehmen der Schuler AG, dem Weltmarktführer in der Umformtechnik, erhielt die Auszeichnung für die beiden Stanzautomaten CSC 1000 und MSC 2000. Durch die ServoDirekt-Technologie bieten die Maschinen eine höhere Ausbringungsleistung, längere Werkzeugstandzeit und verbesserte Energieeffizienz.
„Die verschiedenen Innovationen in der Entwicklung der neuen Antriebstechnologie für Stanzautomaten sowie die damit erreichte Steigerung der Ausbringungsmenge und der Energieeffizienz haben die IHZ-Jury überzeugt”, sagte Jury-Präsident Werner Steinegger. Im Vergleich zu herkömmlichen Maschinen reduziert sich der Energiebedarf der beiden Stanzautomaten, die Beutler Nova zusammen mit Schuler entwickelt hat, um bis zu 50 Prozent.
Die neue Antriebstechnik mit spiel- und schmierölfreien Wälzlagern führt außerdem zu einem geräuscharmen Betrieb. Darüber hinaus lässt sich die Hubbewegung dank ServoDirekt-Technologie in jeder Position unterbrechen und anhalten, was die Integration zusätzlicher Prozesse ermöglicht. Die Funktionen Stanzen, Umformen, Schneiden, Prägen, Biegen sowie Ziehen sind bei der CSC 1000 und der MSC 2000 per Knopfdruck einfach ansteuerbar.
|

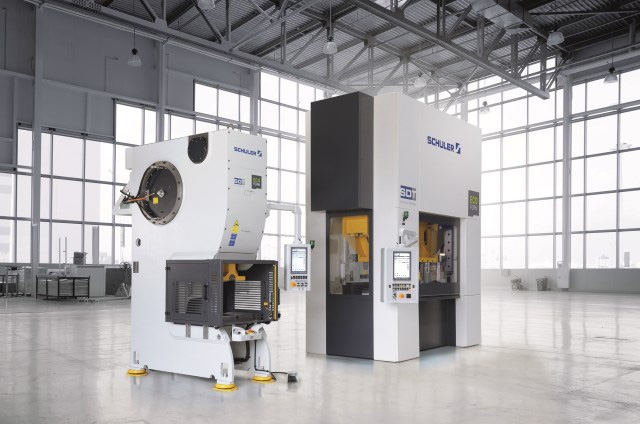
|
|
Oktober
|
|
Das transparente Presswerk
Mit dem Machine Monitoring System legt Schuler zur EuroBLECH ein umfassendes Modell zur Anlagenüberwachung vor
Göppingen, 25.10.2016
In eine Presse lässt sich nicht hineinschauen dabei ließe sich so mancher ungeplante Stillstand vermeiden, wenn sich zum Beispiel ein defektes Teil schon früher bemerkbar machen würde. Das Machine Monitoring System (MMS) der Zukunft, für das Schuler zur EuroBLECH ein Modell präsentiert, gewährt völlig neue Einblicke in Pressen: Mit Hilfe einer umfassenden Anlagenüberwachung lassen sich die Verfügbarkeit erhöhen, die Produktions- und Teilequalität verbessern und der Energiebedarf senken. Das MMS gehört zum Smart Press Shop, in dem Schuler Lösungen zur Vernetzung in der Umformtechnik sammelt.
Schnelle Fehler-Analyse
In dem Modell zur Anlagenüberwachung führt Schuler verschiedene bestehende Lösungen zusammen. Fester Bestandteil des MMS ist die intelligente Diagnose, die physikalische Größen und steuerungstechnische Zustände bei bestimmten Ereignissen automatisch archiviert und auswertet. Das ermöglicht eine schnelle Fehler-Analyse.
Die Zustandsüberwachung kontrolliert die Anlage in regelmäßigen Abständen auf Schäden und Verschleiß, beispielsweise anhand von Drehmomentverläufen und Körperschallanalysen. Dank dieser zustandsorientierte Instandhaltung muss eine Komponente erst dann ausgetauscht werden, wenn es auch tatsächlich an seinem Lebensende angelangt ist und nicht nur deshalb, weil es für eine bestimmte Zeit in Betrieb war.
Verbesserte Prozess-Sicherheit
Bei der Prozessüberwachung steht der Maschinenschutz im Vordergrund. Die permanente Erfassung von Parametern wie dem Presskraft- oder Schwingungsverlauf erlaubt gegebenenfalls eine zyklusgenaue Reaktion in Echtzeit. Dadurch verbessert sich auch die Prozess-Sicherheit.
Zur Energieüberwachung gehört die Erfassung und Auswertung aller Messgrößen, die für die Energieeffizienz und Netzqualität relevant sind wie etwa Leistungsaufnahme, Spannungseinbrüche oder Oberwellen. So können Anlagenbetreiber nicht nur Energiekosten einsparen, sondern unter Umständen auch Investitionszuschüsse und günstige Darlehen erlangen.
Erhöhte Gesamt-Anlageneffektivität
In die Betriebsdatenerfassung fließen alle geplanten und ungeplanten Stillstände einschließlich ihrer Ursachen dafür, die Fehlermeldungen, die Soll-/Ist-Produktion und die Qualität der Teile. Auf diese Weise erhalten die Anlagenbetreiber eine übersicht des Produktionsstatus und die Grundlage zur Berechnung der Gesamt-Anlageneffektivität (Overall Equipment Efficiency oder kurz OEE).
Nicht zuletzt werden für jedes produzierte Teil alle Daten erfasst und archiviert, die für die Qualität maßgeblich sind. Das befähigt den Hersteller dazu, den unter anderem bei Sicherheitsbauteilen erforderlichen Nachweis zu erbringen.
|

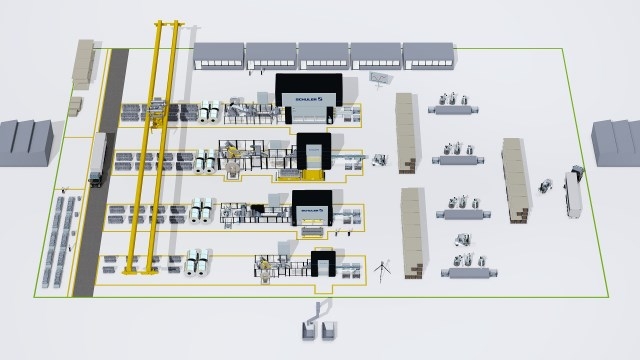 |
|
Oktober
|
|
Neue Service App von Schuler
Per Smartphone können Kunden mit dem Service in Kontakt treten, um direkt an ihrer Anlage kompetente Hilfe zu erhalten
Göppingen, 25.10.2016 Kompetente Hilfe direkt an der Anlage: Die neue kostenlose Service App von Schuler macht genau das möglich. Kunden erhalten über ihr Smartphone rasch Antworten auf ihre Fragen und Hilfe bei der Lösung eines Problems, indem die Experten bei Schuler zum Beispiel Bilder und Videos auswerten, die über die App eingeschickt wurden. Die Software ist Teil des Konzepts Smart Press Shop, mit dem Schuler auf der Fachmesse EuroBLECH in Hannover Lösungen zur Vernetzung in der Umformtechnik präsentiert.
„Mit der Service App können wir unsere Kunden noch besser dabei unterstützen, die Verfügbarkeit ihrer Anlagen zu erhöhen und Stillstände zu minimieren”, sagt Geschäftsführer Axel Meyer, Leiter der Division Service bei Schuler. „Der Dialog mit den Experten von Schuler über die intuitiv bedienbare Software führt in der Regel zu einer schnelleren Problemlösung. über ihr Smartphone erhalten die Kunden von uns eine kompetente Hilfestellung, noch während sie an ihrer Presse stehen. Schneller geht es nicht.”
Mit der Erfahrung von zigtausend installierten Schuler-Pressen im Hintergrund kann der Service anhand der Bild- oder Video-Datei, die der Kunde vor Ort an der Anlage mit der App aufgezeichnet hat, die Ursache oft relativ leicht lokalisieren und im Idealfall gleich beheben. Muss eine Komponente ausgetauscht werden, kann sie der Anwender mit der Kamera seines Smartphones erfassen und mit Hilfe der Teile-Nummer gleich eine Anfrage an den Service schicken.
Bei Bedarf lässt sich auch die Service Hotline aus der App heraus anrufen. Auf Wunsch erhalten die Benutzer darüber hinaus Produktinformationen und Service-News beispielsweise zu Terminen für Schulungen oder Software-Updates für Anlagensteuerungen als Push-Nachrichten auf ihr Handy, um immer auf dem aktuellen Stand zu bleiben.
Die Service App von Schuler ist ab sofort kostenlos als Download für Android-Handys und iPhones erhältlich.
|

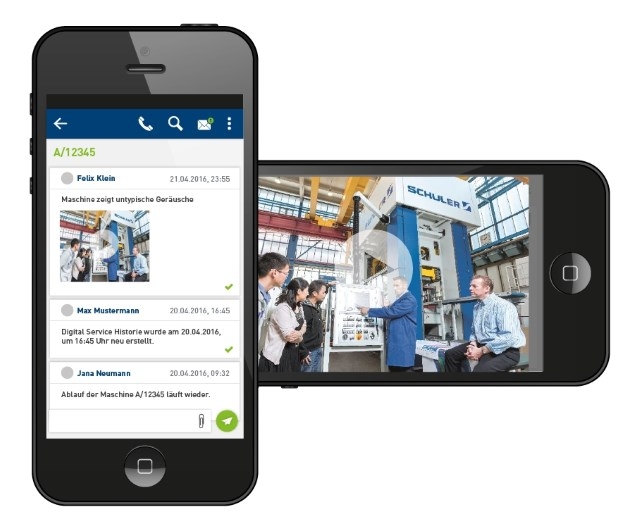
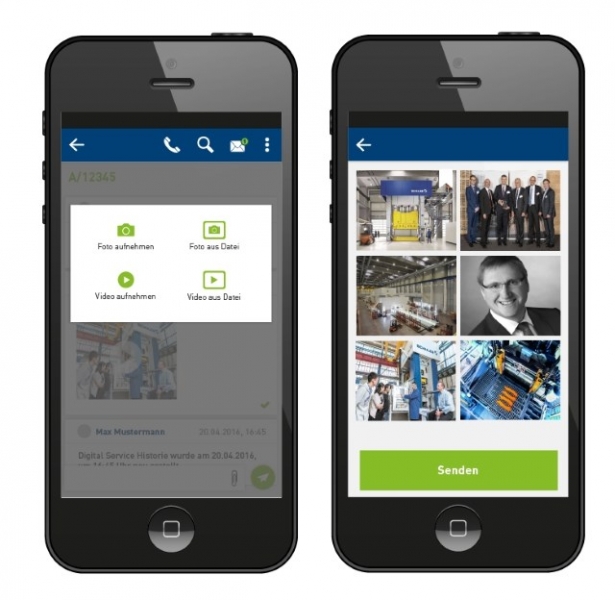 |
|
Oktober
|
|
Hot Stamping TechCenter begeistert Kunden
Über 150 Besucher erleben Formhärte-Anlage neuester Bauart mit einer Ausbringungsleistung von 7,5 Hüben pro Minute in Aktion
Göppingen, 06.10.2016
7,5 Hübe pro Minute, bis zu vier Teile pro Hub und das bei reproduzierbar hoher Qualität: Wie zuverlässig und wirtschaftlich sich mit dem Formhärten hochfeste Komponenten fertigen lassen, haben Kunden von Schuler Ende September im Hot Stamping TechCenter erlebt. über 150 Besucher waren dazu in das Forschungs- und
Vorführzentrum nach Göppingen gekommen, das über eine 1.600 Tonnen starke hydraulische Presse mit PCHflex-Technologie, dazu passendem Werkzeug, Rollen-Herdofen und Twin-Feeder-Automation verfügt.
„Unsere Kunden waren schlichtweg begeistert vom Hot Stamping TechCenter”, freut sich Geschäftsführer Dr. Martin Habert, der die Division Hydraulic bei Schuler leitet. „Ein Besucher hat ein produziertes Teil sogar mitgenommen, um die Genauigkeit selbst überprüfen zu können. Wir haben ihm das Teil gerne mitgegeben, weil wir von der Präzision überzeugt sind, die unsere Technologie bietet.”
Automobilhersteller verbauen immer mehr Formhärte-Teile, weil sie eine
hohe Festigkeit bei geringem Gewicht bieten. In fast jedem Neuwagen
lassen sich mittlerweile formgehärtete A- und B-Säulen, Dachrahmen oder
Verbindungsbleche finden. Bis 2020 verdoppelt sich der Bedarf nach
Angaben von Experten auf 600 Millionen Stück.
Die PCHflex-Technologie von Schuler sorgt für eine schnellere Abkühlung
der auf 930 Grad Celsius erhitzten Teile, weil der Anpressdruck
gleichmäßiger verteilt wird. Das erhöht die Ausbringungsleistung deutlich
und sorgt für einen robusteren Prozess mit konstant hoher
Bauteilqualität. Zur Ausweich- oder Anlaufproduktion lassen sich dabei
ebenfalls konventionelle Formhärte-Werkzeuge auf den PCHflex-Anlagen
einsetzen. So steht auch die Anlage im Hot Stamping TechCenter Kunden
von Schuler für die Einarbeitung von Werkzeugen und die Produktion von
Kleinserien zur Verfügung.
|

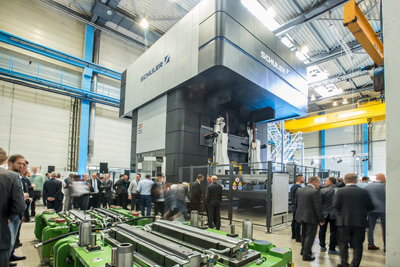
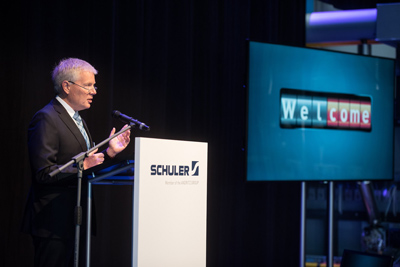
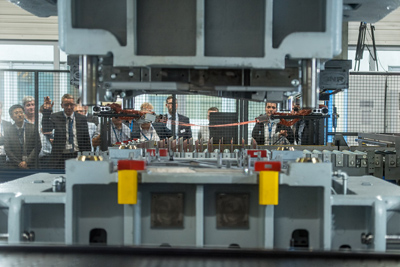 |
|
Oktober
|
|
Smart Assist erleichtert das Einrichten
Elektronischer Assistent im Smart Press Shop von Schuler unterstützt beim Produktionsstart auf Transferpressen und erhöht die Ausbringung
Göppingen, 06.10.2016 Das Einrichten von Transferpressen ist oft eine Angelegenheit für absolute Profis: Presse, Transfer und Bandanlage bei höchster Produktivität in einen harmonischen Einklang zu bringen, erfordert viel Know-how und Fingerspitzengefühl. Der Smart Assist von Schuler erleichtert Pressenbedienern das Einrichten: Schritt für Schritt führt der elektronische Assistent mit Hilfe von Videos und Grafiken durch den Vorgang, optimiert die Bewegungskurven von Stößel und Transfer vollautomatisch und übertragt die Daten an das Gesamtsystem. Schuler stellt den Smart Assist als Bestandteil des Smart Press Shop erstmals auf der Fachmesse EuroBLECH vom 25. bis 29. Oktober in Hannover vor.
„Der Smart Assist beschleunigt das Einrichten von Transferpressen deutlich”, erklärt Technologie-Vorstand Dr. Stephan Arnold. „Die Sicherheit des Teile-Transport ist dabei stets gewährleistet, und die vollautomatische Optimierung der Bewegungskurven einschließlich Beschleunigung und Einstellwinkel erhöht darüber hinaus die Ausbringungsleistung. Damit liefert der Smart Assist innerhalb kurzer Zeit gute Resultate."
Der Smart Assist der zusätzlich zur Pressensteuerung auch auf einem Tablet oder ähnlichem mobilen Endgerät läuft bittet darum, den Stößel und den Transfer nacheinander auf bestimmte Positionen zu fahren. Drückt der Pressenbediener auf „Teach”, werden diese Positionen gespeichert. Auf diese Weise erfasst der Smart Assist den minimal notwendigen Transfer-Hebehub und alle weiteren relevanten Daten. Auf Grundlage der gesammelten Informationen werden anschließend die optimalen Bewegungskurven von Stößel und Transfer
berechnet und die ermittelten Parameter an die Pressensteuerung übermittelt. Der Bediener muss quasi nur noch den Start-Knopf drücken.
Doch die Profis bleiben weiterhin gefragt: Im Experten-Modus erlaubt der Smart Assist die freie Programmierung der Bewegungskurven von Stößel und Transfer etwa für asymmetrische Transferbewegungen zur weiteren Minimierung von Abständen. Damit lassen sich dann auch noch die letzten Prozent bis hin zur maximalen Ausbringungsleistung einer Transferpresse herauskitzeln.
|

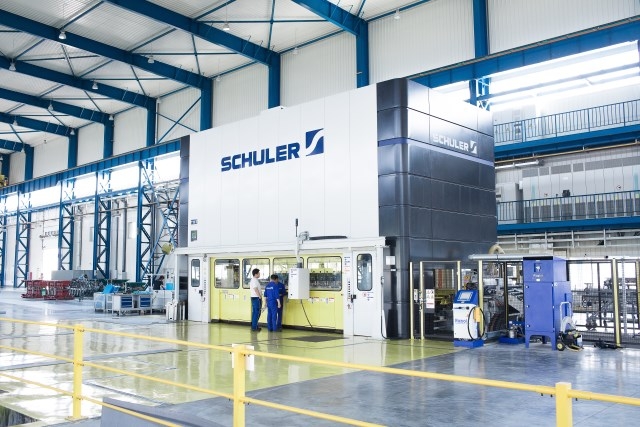
|
|
Juni
|
|
Genauere Teile und weniger Verschleiß
Mit einer TwinServo-Presse von Schuler erhöht Automobil-Zulieferer Fischer & Kaufmann sowohl Produktqualität als auch Werkzeugstandzeit
Finnentrop/Göppingen, 14.06.2016
Automobilhersteller legen großen Wert auf die Präzision der Bauteile, die sie beziehen. Zulieferer wie Fischer & Kaufmann (Fiuka) wissen das ganz genau. Das Unternehmen mit
Sitz im Sauerland verbessert mit einer neuen TwinServo-Presse von Schuler die Genauigkeit seiner Produkte und verlängert die Standzeiten seiner Werkzeuge.
„Wir haben schon mehrere Pressen von Schuler und Müller Weingarten im Einsatz”, berichtet Betriebsleiter Tobias Heutger: „Die Qualität und
Performance stimmen immer.” Mit der TwinServo-Presse verfügt Fiuka nun äber die modernste Anlage am Markt. „Wir sind generell gegenüber neuen Technologien offen eingestellt”, sagt Tobias Heutger. „Letztendlich
war aber das Preis-Leistungs-Verhältnis ausschlaggebend.”
Außen liegende Zugstangen reduzieren Stüßelkippung
So reduziert sich beispielsweise die Stüßelkippung bei TwinServo-Pressen um ein Vielfaches im Vergleich zu herkömmlichen Anlagen. Dieser Effekt ist konstruktionsbedingt: Da sich der Antrieb nicht mehr im Kopfstück,
sondern unter Flur befindet, wird der Stößel von Zugstangen nach unten bewegt. Zusammen mit den spielfreien Führungen erhöhen sich dadurch neben der Prözision der produzierten Teile auch die Prozesssicherheit und
die Werkzeugstandzeiten deutlich. Die außen liegenden Zugstangen sorgen darüber hinaus dafür, dass sich die Maschine mit größeren außermittigen Kräften beaufschlagen lässt.
Seit Dezember vergangenen Jahres steht die 1.600 Tonnen starke Anlage am Standort Finnentrop. Auch wenn sie vier Monate später noch nicht unter Volllast läuft, so lässt sich schon jetzt eine Steigerung der
Produktivität absehen: „Im Vergleich zu unseren konventionellen Pressen können wir die Zahl der Hübe pro Minute von maximal 16 auf jetzt bis zu 34 mehr als verdoppeln”, sagt Betriebsleiter Tobias Heutger.
Die hohe Steifigkeit und geringe Auffederung des Gesamtsystems verringert außerdem den Schnittschlag beim Stanzprozess, die Maschine arbeitet also wesentlich leiser. Ein weiteres Entscheidungskriterium war für Fiuka die niedrige Bauhöhe der TwinServo-Presse, die sich aus dem fehlenden Kopfstück ergibt.
Neuartiger Transfer erhöht Ausbringungsleistung
Doch nicht nur die Presse an sich ist eine technologische Innovation, sondern auch die Automation, die in der Anlage zum Einsatz kommt:
Neben der Bandanlage und dem hochdynamischen Zick-Zack-Walzenvorschub PowerFeed zur optimalen Materialausnutzung lieferte Schuler auch einen neu entwickelten Transfer.
Beim sogenannten IntraFeed sind die Greifer für den Teile-Transport nicht fest an den Schienen montiert, sondern an beweglichen Schlitten, die über einen eigenen Vorschubantrieb verfügen. Dadurch verkürzt sich die Länge der Transferschienen und damit auch die der gesamten Anlage erheblich. Positiver Nebeneffekt: Weil die bewegte Masse sinkt, erhöht sich die Ausbringungsleistung.
Darüber hinaus lassen sich dank der verfahrbaren Schlitten die einzelnen Umformstufen in variablen Abständen anordnen. Das eröffnet neue Freiheiten in der Werkzeugkonstruktion, weil mehr Umformstufen auf dem Pressentisch Platz finden. So ist es denkbar, die Schneidstufe und die folgenden Umformstufen jeweils mit separaten Schlitten zu bedienen. Damit lassen sich die Stufenabstände optimal gestalten.
Fiuka ist von der TwinServo-Presse und dem IntraFeed so überzeugt, dass das Unternehmen noch im vergangenen Jahr die zweite Maschine dieses Typs bei Schuler bestellte. Die baugleiche Anlage wird derzeit ausgeliefert.
|

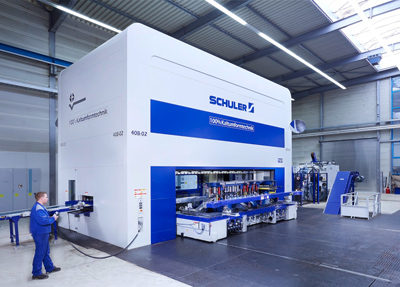
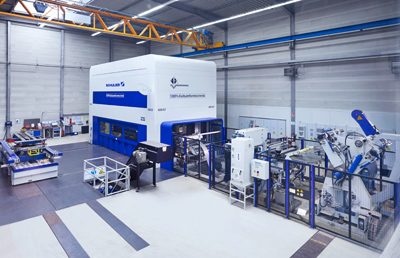
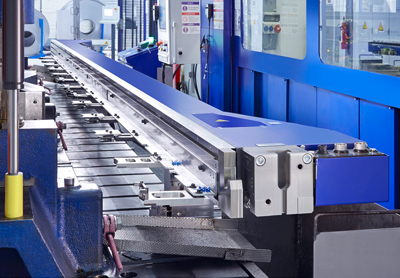
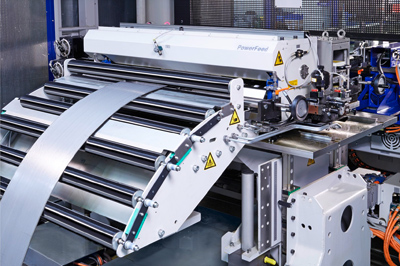 |
|
Juni
|
|
Servopresse sichert Großauftrag
Mit einer vollautomatisierten 630-Tonnen-Servopresse von Schuler hat Brüninghaus & Drissner einen echten Wettbewerbsvorteil
Göppingen/Hilden, 07.06.2016
Als im Frühsommer 2014 beim Automobilzulieferer Brüninghaus & Drissner ein Großauftrag zur Fertigung von Bremspedalen einging, war schnell klar: Mit dem bestehenden Maschinenpark war das aus Kapazitätsgründen nicht zu schaffen. Geschäftsführer Marc-Oliver Köhler entschied sich schließlich für eine Neuanschaffung in Form einer 630 Tonnen starken Servopresse von Schuler und sicherte damit nicht nur den Auftrag, sondern zog von einem anderen Kunden gleich einen zweiten an Land.
Köhler hatte sich die Entscheidung für die Investition nicht leicht gemacht und den Markt genau analysiert: „Aber Schuler ist einfach eine starke Marke in der Umformtechnik. In den Presswerken von Daimler sieht man beispielsweise überall Maschinen von Schuler ”, sagt der 41-Jährige, der bevor er Anfang 2014 die Geschäfte bei Brüninghaus & Drissner übernahm selbst 22 Jahre bei dem Stuttgarter Premium-Automobilhersteller gearbeitet hatte.
Hinzu kamen die guten Erfahrungen, die der Automobilzulieferer mit einer Presse von Müller Weingarten im Maschinenpark gemacht hatte. „Die Anlagen aus dem Schuler-Konzern sind fast so wertbeständig wie ein Porsche”, lacht Köhler, der Autos und Maschinen aus dem Südwesten Deutschlands insgesamt sehr schätzt: „Was aus dem Schwabenland kommt, ist schon echt gut.”
Als bei Brüninghaus & Drissner das Fundament für die Presse zum vereinbarten Liefertermin noch nicht gelegt war, lagerte Schuler die Monoblock-Maschine kurzerhand ein. „Das war eine große Unterstützung für uns”, erinnert sich der Geschäftsführer. „Bei Schuler geht man auf die Kunden ein und ist immer für sie verfügbar. Und selbst wenn mal etwas nicht optimal läuft, wird umgehend nachgebessert. Das ist ganz wichtig für mich.”
ServoDirekt-Technologie eröffnet neue Möglichkeiten
Seit Januar 2016 ist die Servopresse vom Typ MSD-630 einschließlich Bandanlage und Drei-Achs-Transfer im Betrieb. Schuler lieferte das Komplettsystem aus einer Hand. Durch mehr Presskraft, einem vier Meter breiten Tisch und der flexiblen ServoDirekt-Technologie (SDT) eröffneten sich nun ganz neue Möglichkeiten. Vor Ort an der Servopresse führen die Spezialisten von Schuler Anwender-Schulungen durch. So ist gewährleistet, dass Brünninghaus & Drissner die Anlage optimal einsetzen und dadurch deutliche Ausbringungssteigerungen erzielen kann.
„Alle meine Leute bis hin zum Bediener haben sich schnell mit der Anlage angefreundet und sind mittlerweile regelrecht von ihr begeistert”, berichtet Köhler. „Innerhalb von vier Monaten haben wir es geschafft, die Ausbringungsleistung auf 18 Hübe pro Minute zu erhöhen. Und da ist noch viel Luft nach oben. Die bisherige mechanischen Anlage mit Schwungrad-Antrieb hat bestenfalls 13 Hübe pro Minute erreicht.”
Durch den größeren Pressentisch und die hohe Flexibilität der Schuler ServoDirekt-Technologie von Schuler konnte Brüninghaus & Drissner weitere Funktionen in das Werkzeug integrieren, erklärt der Geschäftsführer: „Ein Bremspedal ist sehr kompliziert herzustellen, muss aber absolut fehlerfrei und zu 100 Prozent genau sein. Mit dem erweiterten Werkzeug können wir nun auf einen Arbeitsschritt komplett verzichten. Das bringt uns einen echten Wettbewerbsvorteil.”
Mit der Neumaschine ging der zweite Großauftrag bei Brüninghaus & Drissner ein: „Den haben wir nur wegen der Schuler bekommen”, ist Marc-Oliver Köhler überzeugt. Und auch er denkt schon „intensiv” über die Anschaffung einer zweiten voll automatisierten Servopresse von Schuler nach.
|

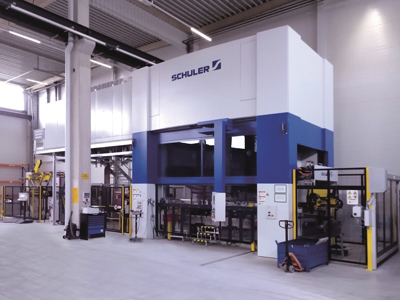
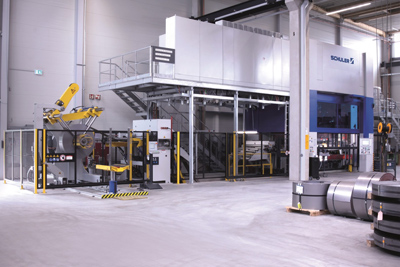 |
|
|
|
|
 |